6 Steps to Using the IoT to Deliver Maintenance Efficiency
The Internet of Things (IoT) and Big Data offer companies the ability to aggregate existing data sources, gain visibility into new data, and identify patterns through analytics to make better business decisions.
August 30, 2016
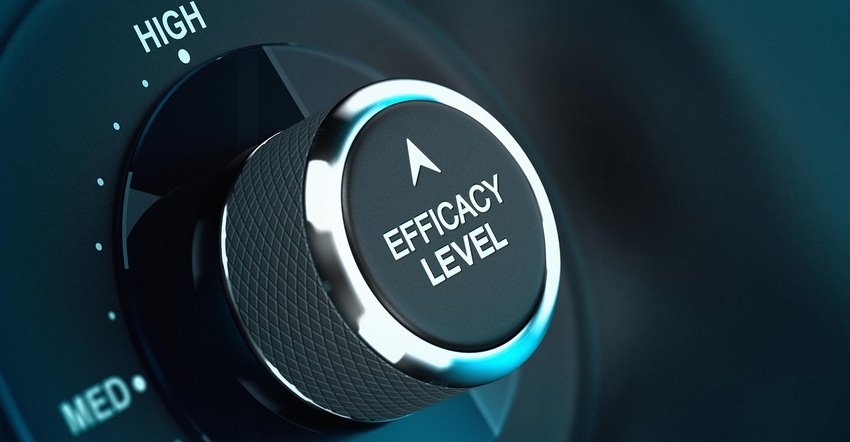
Sponsored Content
According to a recent survey report conducted by the Aberdeen Group, “Best-in-Class” companies are increasingly utilizing IoT and Big Data to implement Predictive Maintenance (PdM) models to address and improve their top operational challenges:
Reduce unplanned downtime by 3.5% – Amount of unscheduled downtime against total availability
Improve Overall Equipment Effectiveness (OEE) to 89% – Availability x Performance x Quality = OEE
Reduce maintenance costs by 13% YoY – Total maintenance costs including time and personnel
Increase return on assets (RoA) by 24% – Profit earned from equipment resources through improved uptime
Any industry that operates “machinery” – manufacturing, transportation, building automation – can benefit from PdM enabled by sensor-generated data.
The value over any other maintenance model is that PdM empowers maintenance and operation decision makers to predict when an asset will need intervention well in advance of its failure impacting personnel, operations or production.
Related: To learn more about Dell’s IoT strategy, check out Dell World.
PdM provides the highest possible visibility of the asset by collecting and analyzing various types of data to provide the following benefits:
Identifying key predictors and determining the likelihood of outcomes.
Optimizing decision-making by systematically applying measurable real-time and historical data.
Planning, budgeting and scheduling maintenance repairs, replacements and spares inventory.
Follow these 6 best practice steps to plan your PdM implementation:
1. Establish the business case for PdM
To make the case for a PdM implementation, the focus should be on the unique problems that affect optimizing operational and production impacts while managing risk. It’s important to understand what metrics the organization is focusing on and which need to be improved. Consider these questions to identify key goals of your PdM project and ensure success:
What critical assets are likely to fail? When and why do we believe they will fail?
How would the assets’ failure impact personnel, operations and or production costs? What does downtime cost?
How can data driven decisions be integrated within the constraints of your existing maintenance practices?
2. Identify and prioritize data sources
The increase in asset connectivity and use of smart devices may have generated large amounts of available data. It is not needed or recommended to address this whole universe of possible data. Instead, begin to predict failures on a single asset by focusing on the usable, existing data sources related specifically to it.
3. Collect selected data
The selected data may reside in disparate locations from a device at the network edge to the server room to the enterprise cloud, including sensors, meters, enterprise asset management systems, and supervisory control and data acquisition (SCADA) systems. An ideal PdM solution should be flexible enough to enable you to collect from all of these data sources to learn and continually make better, more informed business decisions. The Dell Edge Gateway is an industrial-grade, scalable solution for the Edge which works with a variety of critical protocols, data sources, and types of data.
4. Determine where to run your analytics
Establish an advanced analytics foundation based on your specific operation. For example, Edge (or local) and Cloud analytics can be balanced to reduce the burden of streaming perishable PdM data on your cloud deployment. A distributed approach enables you to detect and respond to local events at the edge as they happen, taking action immediately on streaming data, while simultaneously integrating additional data sources in the cloud. The Dell Edge Gateway can analyze streaming data in memory for real time response and filter out unnecessary data rather than relaying it to the cloud.
5. Combine and analyze data to gain precise insights
Start by analyzing data to define the parameters of normal operation for a machine. This enables the creation of rules through condition monitoring for analyzing the real-time data coming directly from machine sensors on the Dell Edge Gateway. With the Edge Gateway, analytics can happen as close to the machine as possible with the native I/O to collect data from industrial equipment and the ability to operate in harsh environments. After analyzing the real-time data, add historical and third party data such as reliability models and logs to uncover meaningful correlations, patterns and trends with the anomalies generated by the real-time data rules, to signal potential failures. The patterns can be used to further refine your rules and offer actionable insights in real time.
6. Operationalize and take action
Turn insights into action by integrating an aggregated risk assessment for all assets into your operation through a single dashboard. For example, when a potential problem is uncovered the Dell Edge Gateway triggers an event that allows you to send out automated alerts to concerned parties, such as location, estimated replacement parts, and recommended corrective action to avoid a catastrophic event. Then, by capturing wear characteristics data from the replaced parts, you are able to continuously refine your PdM models and learn from performance insights. Finally, explore additional uses for your PdM data such as automating inspection reports and enhancing component supplier evaluation.
To access the full solution brief for predictive maintenance, click here.
You May Also Like